Effect of Relative Density and Gap of Sputtering Target on Large Area Coating
views, Updated: 2021-09-14
As a large raw material for coating, the sputtering target's characteristics, including target shape, purity, density, porosity, grain size, and binding quality, greatly influence film quality and sputtering rate. Here we explain the influence of the relative density and gap of the sputtering target on large-area coating.
Effect of target relative density on large area coating
The target's relative density is the ratio of the actual density of the target to the theoretical density. The theoretical density of the single component target is the crystal density. The theoretical density of the alloy or mixture target is calculated by each component's theoretical density and its proportion in the alloy or mixture. The target structure of thermal spraying is loose and porous with high oxygen content (even in vacuum spraying, it is difficult to avoid the generation of oxides and nitrides in the alloy target). The surface is gray and lacks metallic luster. The adsorbed impurities and moisture are the primary pollution sources, which hinder the rapid acquisition of high vacuum, quickly lead to discharge in the sputtering process, or even burn the target. Figure 1 shows the initial stage of installation and uses the photos of spray target with low density are seriously discharged and burnt out.
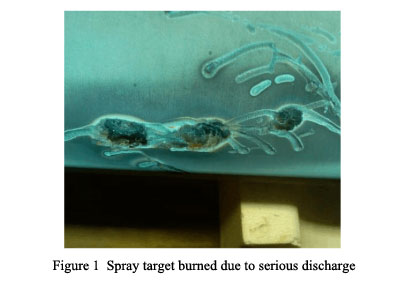
Simultaneously, the high temperature on the target's sputtering surface quickly causes the loose particles to fall, contaminates the glass surface, and affects the coating quality. The higher the relative density, the faster the film-forming rate, and the more stable the sputtering process. According to the difference of target preparation technology, the casting target's relative density should be more than 98%, and the powder metallurgy target should be more than 97% to meet the production use. Therefore, the target density should be strictly controlled to reduce the occurrence of slag dropping. The density of the spraying target is low, and the cost of preparation is also low. When the relative density can ensure more than 90%, it generally does not affect the use.
The effect of target gap on large area coating
In addition to densification, if the target is abnormal in the production process, large particles fall off or shrinkage holes due to heat. As a result, more pores (internal defects) will be formed, and larger or denser pores in the target will be discharged due to charge concentration, affecting the use.
The target with low density, and the air hole is easy to break when processed, transported, or installed. The target with high relative density and few pores has good thermal conductivity. The heat on the sputtering target's surface is easy to be transferred to the cooling water on the inner surface of the target or liner quickly, which ensures the film-forming process's stability.
AEM Deposition, as a professional sputtering target manufacturer, supplies all kinds of pure metal sputtering target, alloy sputtering target, and ceramic compound sputtering target. Further details are as follows:
If you are interested, you can click the relevant link and visit the product page. You can also email us at
[email protected].
LATEST NEWS
2025-05-29
2025-05-22
2025-05-09
2025-04-09
2025-04-09