Effect of Crystal Size and Direction of Sputtering Target on Large Area Coating
views, Updated: 2022-09-29
Target shape, purity, density, porosity, grain size, and binding quality greatly influence the quality and sputtering rate of large-area coating. Here we explain the influence of the sputtering target's crystal size and crystal direction on large-area coating.
The effect of sputtering target grain size on large area coating
For the same composition target, the target's deposition rate with smaller grain size is faster than larger grain size. This is because the grain boundary is more vulnerable to attack in the sputtering process. The more the grain boundary, the faster the film formation. The size of grain size affects the rate of splashing and affects the film quality.
The effect of grain size on the uniformity is small. The results show that four metal targets of the same material prepared by the same preparation process change the grain size from 0.5 to 3.3 mm by different heat treatment time. It is found that there is no difference in the uniformity of the film. Therefore, the grain size has little or no effect on the film uniformity.
However, the uniformity of grain size will directly affect the uniformity of film formation. Given the continuous consumption of the target, in addition to the uniformity of the same layer of the target, the uniformity of the target thickness direction should also be considered, and the grain size of different sections should be as consistent as possible to ensure the uniformity of film formation in different periods.
Figure 1 shows the microstructure comparison of NiCr sputtering targets from different manufacturers. From the crystal phase photos, it can be seen that the grain size and uniformity of target a are better than that of target b, and the quality of target a corresponding to the sputtered film is higher.
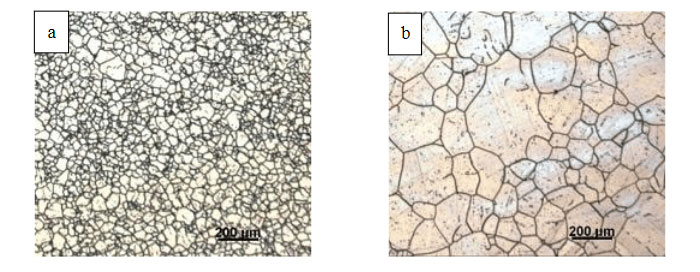
Figure 1: Comparison of microstructure of Ni-Cr target
Effect of crystal direction of sputtering target on large area coating
For polycrystals, the crystal grains are arranged along some special orientations in different degrees. In the target sputtering process, the low-energy ions can not directly splash out atoms from the solid surface but transfer the momentum to the collided atoms, causing the lattice atom chain collision. This kind of collision will be carried out along all directions of the crystal lattice, but it is most effective in the order of the most closely arranged lattice of atoms.
Therefore, the atoms on the target surface are easy to be sputtered out along the direction of the closest arrangement of atoms. The crystal direction of the material has a significant influence on the sputtering rate and film thickness uniformity. We can improve the shooting rate and film quality by changing the crystal structure of the target. For example, the film thickness deviation can be reduced from 10% to 5%.
Different materials have different crystal structures, so other methods and conditions of forming and heat treatment should be used to process them so that the target material has the best crystal orientation. The film-forming rate and film quality can be improved by magnetron sputtering.
AEM Deposition, as a professional sputtering target manufacturer, supplies all kinds of pure metal sputtering target, alloy sputtering target, and ceramic compound sputtering target. Further details are as follows:
If you are interested, you can click the relevant link and visit the product page. You can also email us at
[email protected].
LATEST NEWS
2025-05-29
2025-05-22
2025-05-09
2025-04-09
2025-04-09